Una casa mal aislada es la vía más rápida para tener abultadas facturas de calefacción y aire acondicionado cada mes. De hecho, cerca del 25% de la energía que se produce en todo el mundo se utiliza para calentar y refrigerar viviendas y edificios comerciales, según datos del Climate Portal del MIT. Por eso es fundamental el desarrollo de nuevos materiales de construcción para proporcionar un mejor aislamiento y reducir tanto el consumo de energía como las contribuciones al calentamiento global.
En la búsqueda de alternativas sostenibles al cemento convencional, que representa el 8% del total mundial de emisiones de CO2, los investigadores de la Universidad de Newcastle (Inglaterra) han desarrollado un nuevo mortero ecológico que promete mejorar la eficiencia energética en la construcción y, además, reducir el desperdicio de plástico.
El equipo de investigación ha creado una mezcla de mortero que sustituye la arena tradicional por aerogel de sílice y plástico PET reciclado, el que se suele utilizar para la fabricación de botellas. El aerogel de sílice es reconocido por sus altas propiedades aislantes y se utiliza cada vez más en sectores como la construcción y la industria aeroespacial. Al incorporar estos materiales, el nuevo mortero no solo mejora el aislamiento térmico, sino que también reduce el peso de la estructura.
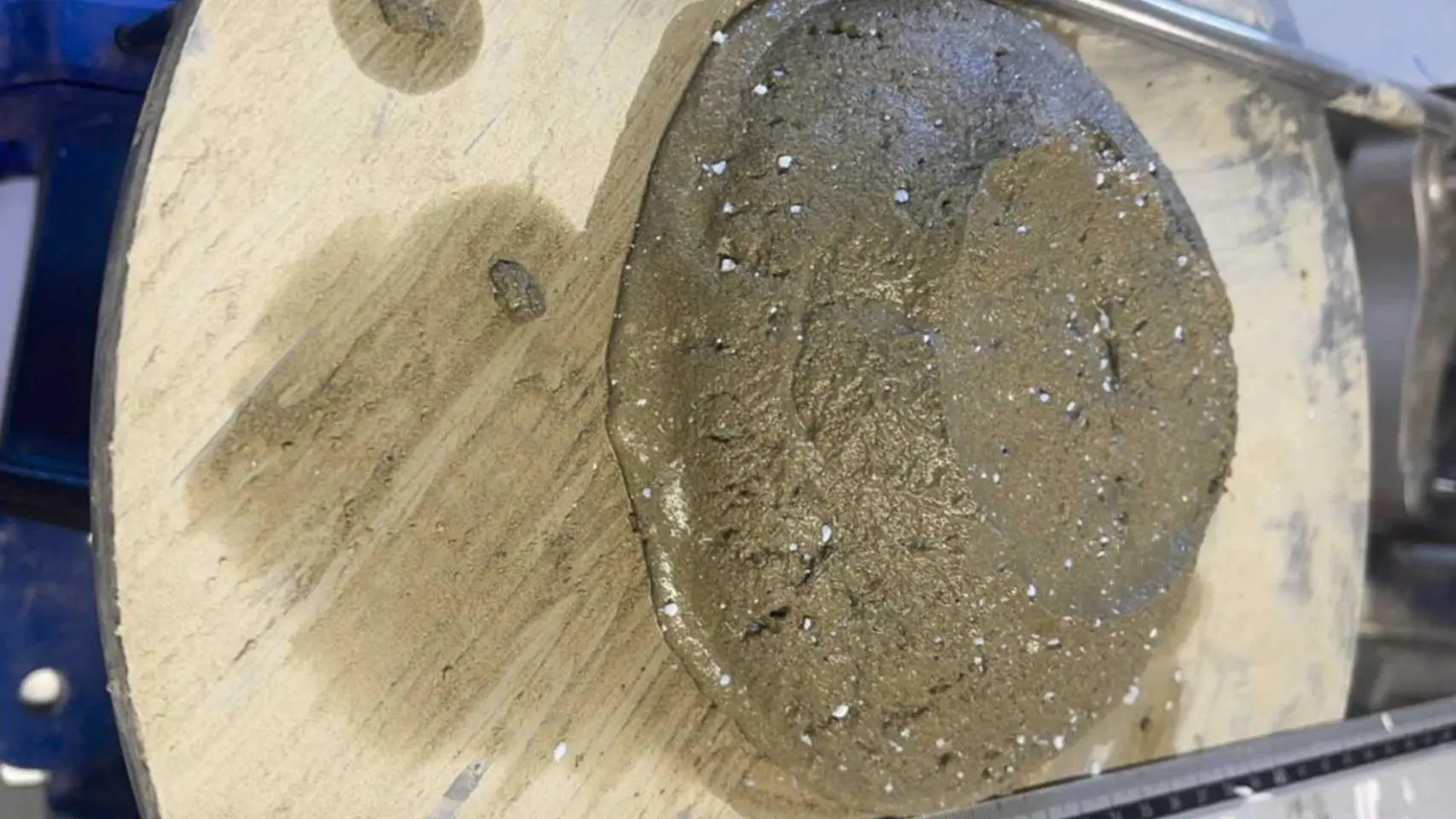
Una de las pruebas con el nuevo mortero desarrollado por investigadores de la Universidad de Newcastle
Según los resultados publicados en la revista Construction and Building Materials, esta innovadora mezcla puede reducir la pérdida de calor hasta en un 55% en comparación con el mortero convencional, manteniendo la resistencia necesaria para la construcción de edificios de mampostería. Además, cumple con los estándares internacionales, posicionándose como una alternativa ecológica para edificaciones energéticamente eficientes y sostenibles.
La profesora Lidija Šiller, especialista en Ciencia a Escala Nanométrica en la Escuela de Ingeniería de la Universidad de Newcastle y coautora principal del estudio, destacó la relevancia de este desarrollo en un comunicado de prensa: «Este estudio demuestra que nuestra formulación de residuos plásticos de PET reciclado puede utilizarse para producir morteros a base de cemento, y es una forma efectiva de reducir su impacto en el medio ambiente«.
Pruebas y experimentos
El proceso de fabricación del nuevo mortero involucró la prueba de siete formulaciones diferentes junto con mortero tradicional. La combinación más efectiva resultó ser la que reemplazaba el 7% de la arena natural por aerogel de sílice no tratado y añadía un 3% de plástico PET reciclado a la mezcla. Las partículas de PET utilizadas provenían de botellas de plástico trituradas, presentando formas irregulares y tamaños de entre 2,5 y 5 mm.
La implementación de este mortero ecológico podría transformar las prácticas constructivas actuales, ofreciendo edificaciones más eficientes energéticamente y con una menor huella ambiental. Además, al reducir la dependencia de materiales tradicionales y aprovechar residuos plásticos, se promueve una economía circular en la industria de la construcción.
Aún así, queda mucho trabajo por delante, ya que la combinación de plástico PET reciclado y aerogel de sílice hace que la mezcla de cemento sea menos manejable y más difícil de trabajar, debido a la naturaleza hidrofóbica de ambos materiales. Además, la mezcla resultante reduce la resistencia a la compresión, debido a la débil adhesión entre el plástico y el cemento, lo que genera microespacios en la mezcla y lo hace más quebradizo.
A pesar de estos aspectos a mejorar, los resultados obtenidos en entornos controlados permiten a los investigadores ser optimistas, ya que el material cumple con los requisitos de los estándares internacionales.
En cualquier caso, todavía queda la prueba de fuego: usar la nueva mezcla en un entorno real y a gran escala. «Para el siguiente paso, queremos encontrar colaboradores, como una empresa constructora, que solicite financiación y construya la casa con nuestra receta de mortero«, asegura Šiller. «Esto nos permitirá aportar pruebas directas del ahorro energético potencial y evaluar los aspectos económicos de las aplicaciones en edificios de mampostería«, concluye.
Materiales aislantes
En los últimos años, científicos y compañías especializadas en construcción han redoblado los esfuerzos para conseguir materiales de construcción capaces de mejorar el aislamiento de los edificios. Empresas como la francesa Isover se han centrado en desarrollar productos como Isocoton. Este aprovecha los residuos textiles como ingrediente principal de paneles de aislamiento con excelentes propiedades tanto térmicas como acústicas.
Así, además de promover el respeto por el medioambiente, se obtienen productos muy competitivos, en algunos casos con mejores prestaciones que los más habituales, como la lana de roca, la espuma de poliuretano o el poliestireno. Partiendo de un 70% de algodón reciclado, un 15% de textiles sintéticos y otro 15% de fibras de poliéster que ejercen como aglutinante, el proceso para convertir ese material en paneles aislantes para la construcción implica el uso de calor y se realiza en seco.
El resultado tras todos los procesos de transformación son unos paneles duraderos y flexibles de 120 cm de largo y 60 cm de ancho, que se pueden instalar fácilmente por los profesionales en paredes, tabiques y techos, con una reducida conductividad térmica de entre 0,037 y 0,051 W/m.K.
En esa misma línea, un equipo de investigadores de la Universidad Tecnológica de Panamá (UTP) ha comprobado la eficacia de un material aislante a base papel de periódicos reciclado y cáscara de arroz. Este último es un producto muy habitual en el país centroamericano, donde se considera un residuo agrícola y habitualmente acaba incinerado o en vertederos, con lo que se desaprovecha su potencial para nuevos usos.
Los investigadores decidieron poner a prueba sus propiedades aislantes triturando las cascarillas del arroz para conseguir partículas de 0,6 mm y añadiéndole celulosa obtenida de periódicos reciclados y triturados. A la mezcla se agregó cola, para dar consistencia, y bórax, encargado de convertir la masa resultante en paneles térmicos para la construcción resistentes a los hongos y con propiedades ignífugas.
De momento, todo forma parte de un work in progress, y tampoco se descarta la inclusión de otros elementos naturales en la mezcla, como fibras largas que apunten en una dirección concreta con el fin de reforzar el comportamiento del material cuando es sometido a tensión.